1. What Happened
A customer’s critical shipment, destined for a grocery store, was unexpectedly involved in a road accident while en route to its destination. The incident created an immediate risk of delivery delays, potential product loss, and additional costs for both the customer and the carrier. Fortunately, upon inspection, it was determined that the cargo itself had not sustained any damage during the accident.
2. How It Happened
The shipment was being transported via truck when the vehicle was involved in a traffic accident. While the specifics of the accident (such as weather, road conditions, or driver error) were not detailed, the incident resulted in the truck being rendered inoperable and required towing to a secure facility. This situation posed several logistical challenges, including the need to quickly recover the intact cargo, coordinate with third-party tow and recovery services, and avoid any unnecessary storage or delay fees that could further impact the customer.
3. What Could Have Been Done to Prevent It
While accidents are sometimes unavoidable, several proactive measures can help minimize risk:
- Enhanced Driver Training: Regular safety training and defensive driving courses can reduce the likelihood of accidents.
- Route Planning: Utilizing advanced route optimization tools to avoid high-risk areas or hazardous weather conditions.
- Vehicle Maintenance: Routine inspections and maintenance can prevent mechanical failures that might contribute to accidents.
- Telematics and Monitoring: Real-time vehicle tracking and monitoring can provide early warnings of unsafe driving behaviors or environmental hazards.
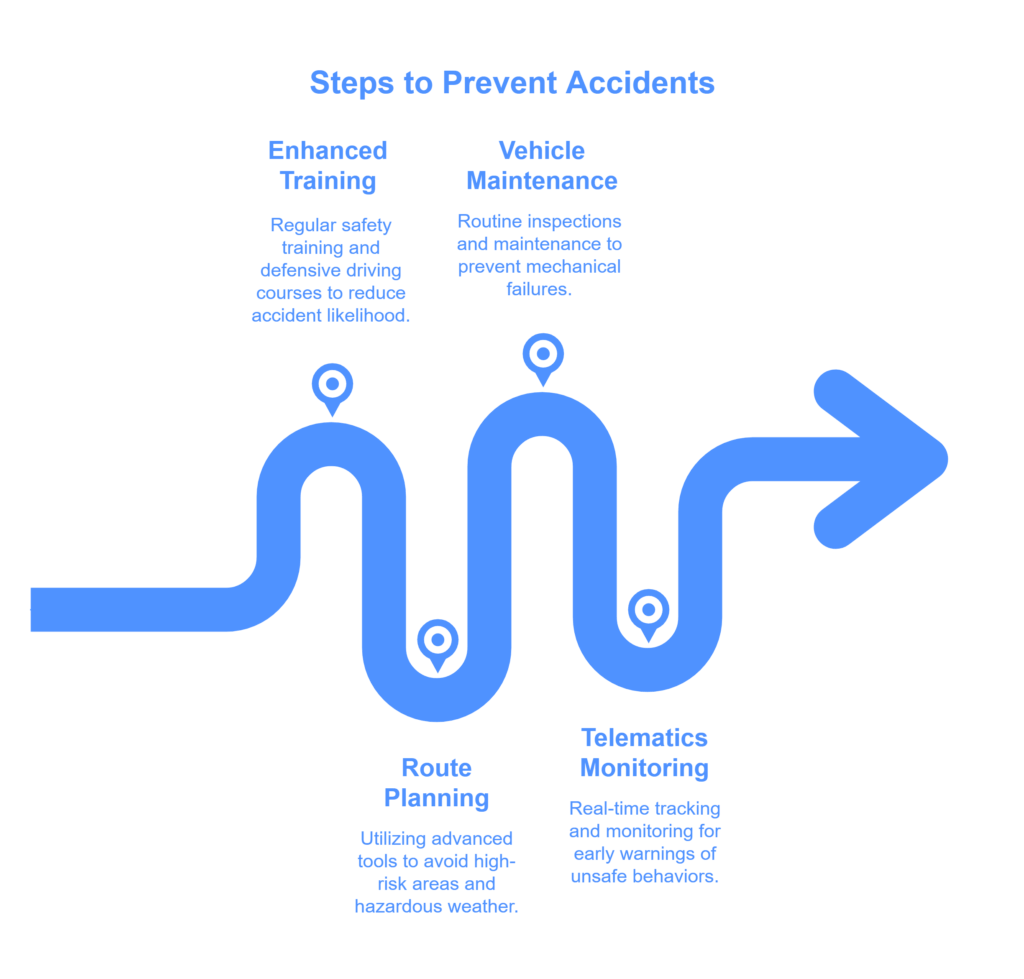
While these steps cannot eliminate all risks, they can significantly reduce the chances of similar incidents occurring in the future.
4. How SPI Solved the Problem
SPI Logistics demonstrated exemplary crisis management and customer service in response to the incident:
- Immediate Action: Upon learning of the accident, SPI quickly secured a recovery carrier and coordinated with the tow facility to arrange for the cargo to be transloaded onto a recovery trailer.
- Cost Control: SPI negotiated approval for the transloaded shipment to remain at the facility overnight without incurring additional storage charges, ensuring that costs remained under control.
- Proactive Communication: Throughout the process, SPI maintained consistent and transparent communication with all involved parties, including the customer, the tow facility, and the recovery carrier.
- Timely Delivery: By orchestrating the early morning pickup of the shipment, SPI ensured the cargo was released promptly and delivered to the grocery store on schedule, despite the unforeseen disruption.
- Overcoming Industry Challenges: SPI’s ability to facilitate the release of cargo from a tow facility within a day is notable, as such situations often involve bureaucratic delays and logistical hurdles.
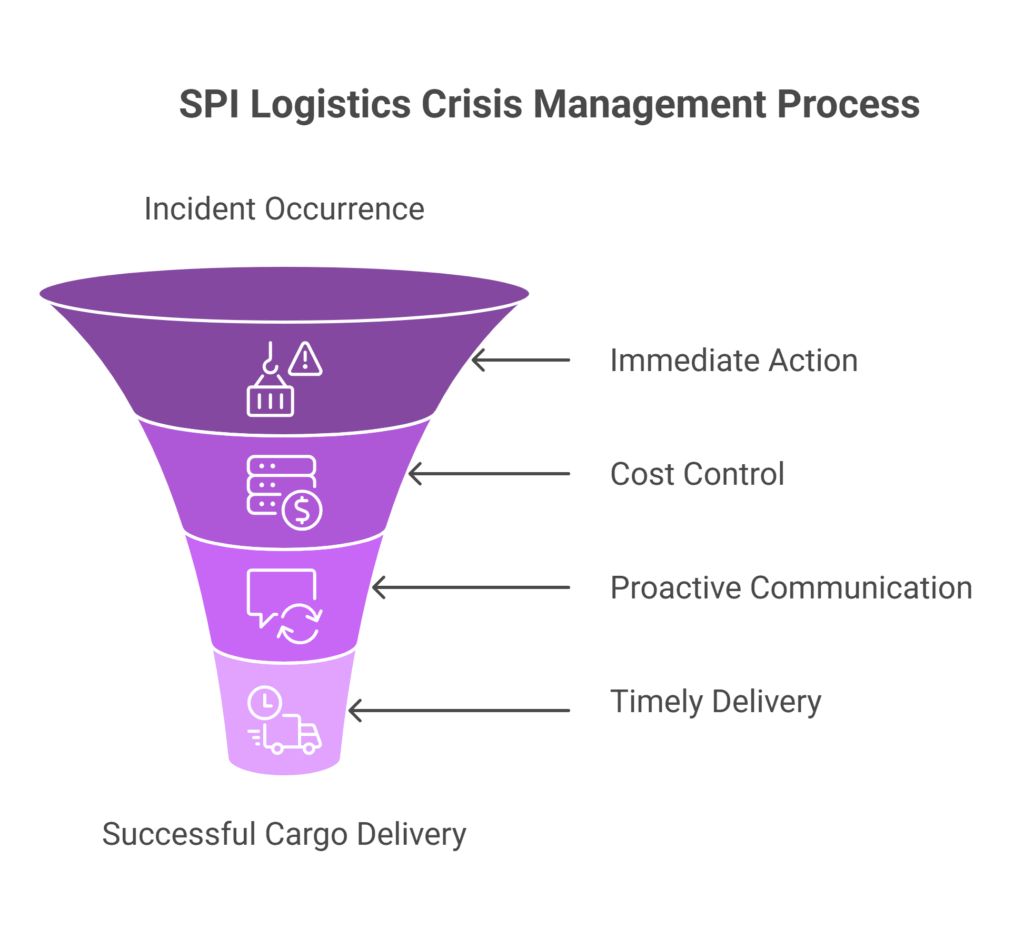
Key Lesson:
This incident highlights SPI Logistics’ commitment to operational excellence, proactive problem-solving, and customer satisfaction. Through swift action, clear communication, and effective coordination, SPI not only mitigated the impact of an unexpected accident but also ensured the customer’s shipment arrived on time, demonstrating why they are a trusted partner in logistics.