Staying ahead of the competition means having a warehouse that operates like a well-oiled machine. But how can you be sure your warehouse is performing at its best? That’s where Key Performance Indicators (KPIs) come in. Understanding and tracking the right warehouse KPIs allows you to pinpoint areas of improvement, boost efficiency, and optimize your overall operations (ASCM, n.d.).
But which KPIs should you focus on? And how can you apply them effectively to your warehousing and logistics processes? Let’s break it down together.
What Are Warehouse KPIs and Why Do They Matter?
At their core, warehouse KPIs are measurable values indicating how effectively your warehouse performs. These metrics give you insight into key operational areas, such as inventory accuracy, order processing, and receiving times [ShipBob: 23 Warehouse KPIs and Metrics to Improve Performance]². By regularly tracking these KPIs, you’ll be able to:
- Identify bottlenecks
- Improve operational efficiency
- Increase profitability
- Ensure customer satisfaction
Now, let’s dive into the most important warehouse KPIs every logistics professional should track (Modula USA, n.d.).
Top Warehouse KPIs to Track
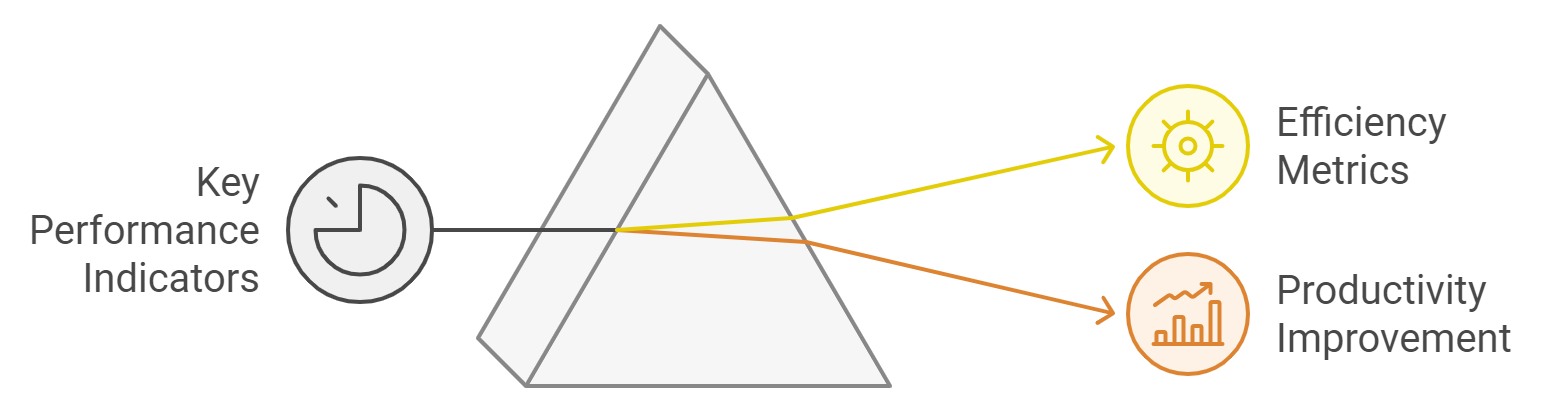
Here are the key performance indicators that matter most in warehousing and logistics [Veeqo: 7 Warehouse KPIs You Need to Start Tracking in 2024]⁴:
1. Order Accuracy Rate
How often are the right products shipped to the right customers on time? Your order accuracy rate tells you the percentage of orders shipped without error. High accuracy keeps your customers happy and reduces costly returns.
- Formula: (Correct Orders / Total Orders) x 100
- Why It Matters: Accurate orders mean fewer customer complaints, less rework, and better customer retention (ASCM, n.d.).
Pro Tip: Are you struggling with order accuracy? Try implementing barcode scanning technology to minimize human error (ShipBob, n.d.).
2. Inventory Turnover
This metric tells you how often your inventory is sold and replaced. A high inventory turnover rate signals strong demand, while a low rate might indicate excess stock or inefficiencies in inventory management (ShipBob, n.d.).
- Formula: Cost of Goods Sold / Average Inventory
- Why It Matters: Efficient inventory management decreases storage costs and frees up space for faster-moving products (Zoho Inventory Academy, n.d.).
Did You Know?: Many warehouses use real-time inventory tracking systems to stay on top of stock levels and streamline reordering (Veeqo, n.d.).
3. Order Cycle Time
The order cycle time measures the average time it takes to fulfill an order, from when it’s placed to when it’s shipped. The faster your cycle time, the more efficient your warehouse is (Modula USA, n.d.).
- Formula: Time from Order Placement to Order Shipment
- Why It Matters: Shorter cycle times improve customer satisfaction and allow you to process more orders in less time (ShipBob, n.d.).
Challenge: Is your order cycle time lagging? Consider investing in automation technologies, such as conveyor or pick-to-light systems, to speed things up (Veeqo, n.d.).
4. Warehouse Capacity Utilization
This KPI measures how efficiently your warehouse space is being used. It compares the space taken up by goods versus the total available warehouse space (Zoho Inventory Academy, n.d.).
- Formula: (Used Space / Total Warehouse Space) x 100
- Why It Matters: Maximizing warehouse space helps reduce costs and avoid the need for additional storage facilities (Modula USA, n.d.).
Quick Tip: Review your racking and stacking systems. Proper space utilization can save you thousands of dollars annually in storage costs (ShipBob, n.d.).
5. Receiving Efficiency
The speed and accuracy with which your warehouse can receive, unload, and store goods is a crucial performance metric. Efficient receiving ensures that products are available when needed without bottlenecks (Veeqo, n.d.).
- Formula: Total Time for Receiving / Number of Shipments Received
- Why It Matters: Streamlining receiving operations prevents slowdowns and ensures your supply chain runs smoothly (Modula USA, n.d.).
Solution: Optimize your receiving processes by pre-scheduling delivery times and investing in automated palletizing systems (Veeqo, n.d.).
6. Picking Accuracy
Picking accuracy measures how often the correct items are selected during the order fulfillment. Mistakes in picking can lead to delayed shipments, increased returns, and dissatisfied customers (ASCM, n.d.).
- Formula: (Correctly Picked Orders / Total Orders) x 100
- Why It Matters: High picking accuracy ensures customer orders are fulfilled correctly, reducing the need for costly returns or corrections (ShipBob, n.d.).
Are you not sure if your picking processes are up to speed? Consider using a warehouse KPI dashboard to track your accuracy in real time and spot issues before they escalate (Veeqo, n.d.).
How to Use a Warehouse KPI Dashboard
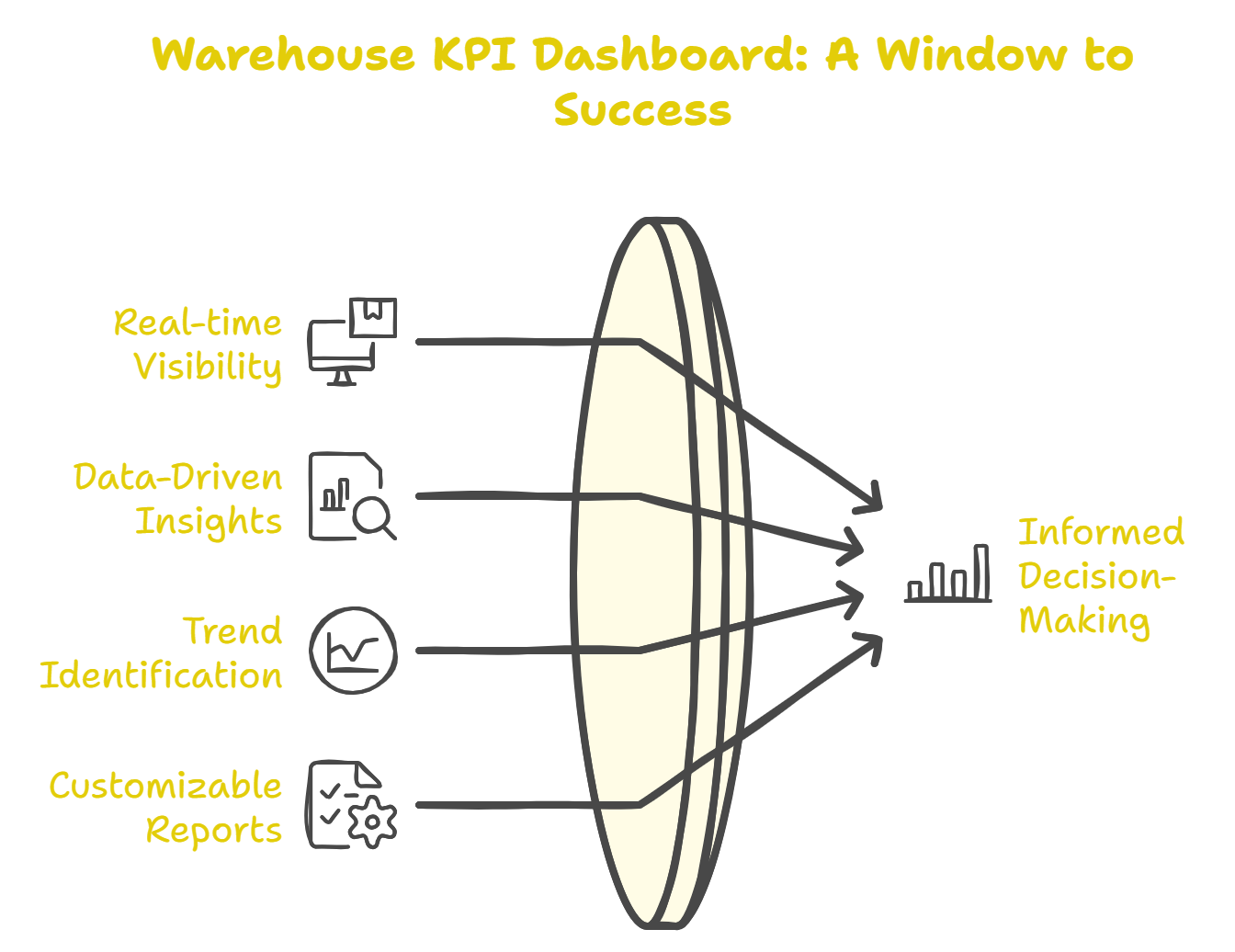
A warehouse KPI dashboard is a valuable tool that allows you to visualize and monitor all your key performance metrics in one place. Whether it’s tracking picking accuracy or monitoring your order cycle times, a dashboard provides real-time insights into warehouse operations, helping you make informed decisions faster (Veeqo, n.d.).
Benefits of Using a KPI Dashboard:
- Real-time visibility of operations
- Better decision-making through data
- Easier identification of trends and potential issues
- Customizable reports tailored to your specific KPIs
Potential Challenges and Solutions
Even with the best KPIs, challenges will arise in any warehouse. Here’s how to tackle a few common ones:
-
Problem: Low inventory turnover leads to excess stock.
- Solution: Conduct regular inventory audits and forecast demand accurately to avoid overstocking (Veeqo, n.d.).
-
Problem: High error rates in picking or packing.
- Solution: Thoroughly train your staff on best practices and implement technologies like voice-picking or automated sorting (ASCM, n.d.).
- Problem: Lengthy order cycle times slow down fulfillment.
Solution: Automate repetitive tasks and invest in technology like warehouse management systems (WMS) to speed up operations (Modula USA, n.d.).
Final Thoughts
Staying on top of your warehouse performance indicators is essential to running a successful operation (Modula USA, n.d.). By regularly tracking KPIs such as order accuracy, inventory turnover, and receiving efficiency, you’ll gain deeper insights into your warehouse’s performance and be able to optimize processes for maximum efficiency (ShipBob, n.d.).
Ready to take the next step? Whether you’re looking to streamline operations or boost customer satisfaction, keeping an eye on these KPIs will give you the tools you need to succeed (ASCM, n.d.). Need help implementing these strategies? Contact us today to learn more about how SPI Logistics can help optimize your warehouse performance!
Want to learn more about warehouse optimization? Check out our latest guide on best practices for warehousing and logistics, or contact one of our experts today!
Focusing on these essential warehouse KPIs can unlock new levels of performance and efficiency in your logistics operations.
References
ASCM. (n.d.). 8 KPIs for an efficient warehouse. https://www.ascm.org
Modula USA. (n.d.). 30 warehouse KPIs to track and measure performance. https://www.modula.com
ShipBob. (n.d.). 23 warehouse KPIs and metrics to improve performance. https://www.shipbob.com
Veeqo. (n.d.). 7 warehouse KPIs you need to start tracking in 2024. https://www.veeqo.com
Zoho Inventory Academy. (n.d.). 21 essential warehouse KPIs to measure performance. https://www.zoho.com